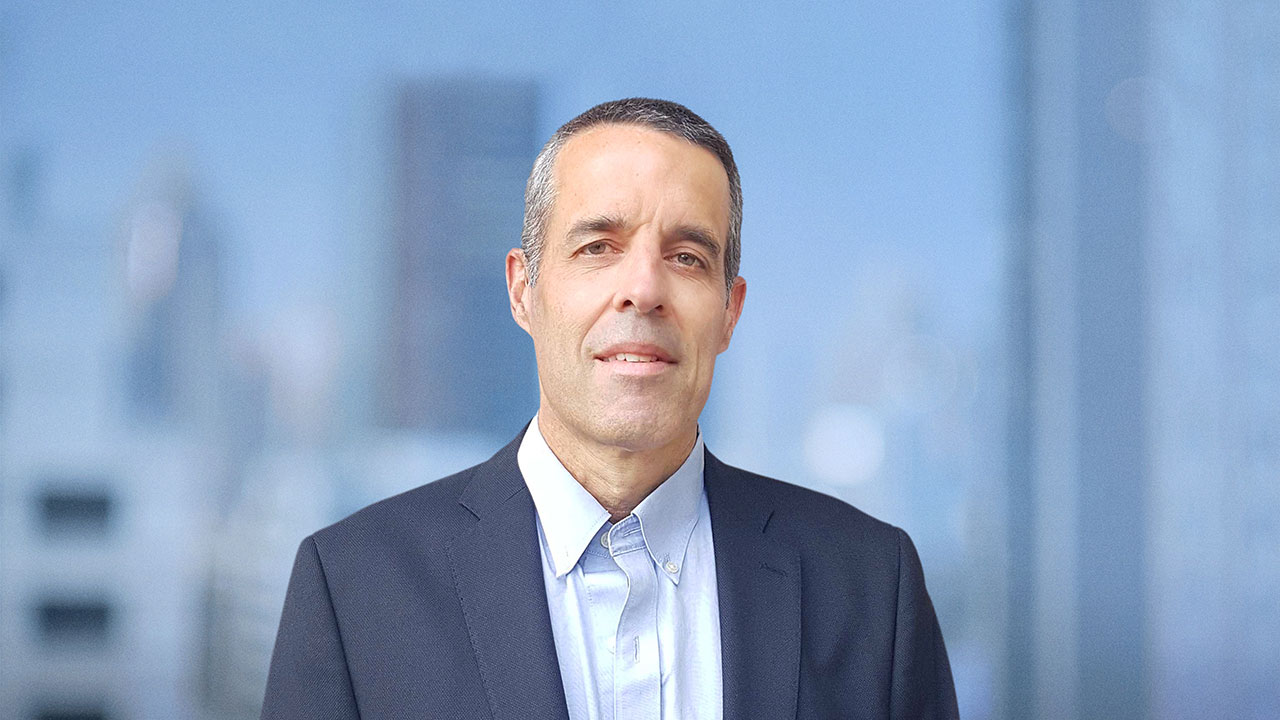
Dr. Wayne Brown, head of innovation and intellectual property at Coanda, A Tetra Tech Company, has worked in process engineering for more than 30 years, applying fundamental chemical engineering principles to challenges in diverse fields such as industrial water, mineral and oil processing, and biotechnology.
Wayne is involved in the development process from all sides, through his roles as a process engineer in an operating plant, as a researcher in industrial research, as a tenure-track professor in chemical engineering at McGill University, and as an entrepreneur developing and advancing his own proprietary technologies.
Most of his efforts are focused on product and process development, intellectual property management, technology development, and process scale-up. In 2011 he was awarded the prestigious ASTech Award for his innovations in oil sands research. Throughout his career Wayne has published several refereed journal articles focused on capturing the complex interaction between biological systems and their chemical environment in a concise mathematical framework.
Wayne holds a PhD in Chemical Engineering from McGill University and is registered as a professional engineer in British Columbia and Alberta, Canada. He has served on the Board at the Canadian Society of Chemical Engineering.
How can models help solve complex water and wastewater problems?
Models provide a convenient means to distill fundamental science into a concise summary of the issue at hand. They can be used to test the validity of the problem analysis and ultimately, if proven to be correct, can be used to evaluate the impact of process changes.
The models we generate at Tetra Tech enable our clients to identify the root cause of a problem and develop a strategy to overcome it, regardless of the problem’s complexity. This is accomplished by coupling our understanding, stemming from decades of experience with process modeling, with advanced measurement techniques to validate conclusions. For example, we have developed mathematical models of novel wastewater treatment technologies based on small-scale results and then used these models to evaluate what commercial deployment strategy would be most appropriate.
What kinds of models exist and what are their limitations?
We apply two broad categories of modeling approaches: physical and mathematical. Physical models that are scaled using real or analog materials to capture the key physics driving the process are extremely useful in visualizing the phenomena underpinning a problem. Mathematical models often are used in conjunction with physical models. It is rare for a problem to be solved using only one modeling approach.
Process modeling often is used to predict the behavior of processes before they are built. Widely used industry standards, including BioWin, are particularly well suited to modeling a range of common process conditions. Such tools fall short when clients try to develop or troubleshoot completely new applications, processes, and geometries that are not considered by commercial packages such as BioWin. This is where our modeling expertise and significant infrastructure resources come together to offer our clients unparalleled insight into their process challenges.
Our experts in numerous disciplines—chemical engineering, applied mathematics, physics, mass transportation, biochemical engineering, fluid dynamics, geotechnical engineering, and more—develop a conceptual model of governing processes and use that as the basis for describing the system. We then develop a pragmatic modeling strategy customized to our clients’ needs and constraints for their process.
How have modeling techniques evolved to keep up with ever-increasing demands?
Scaled physical modeling is a powerful technique for capturing the physics of extremely complex processes. Exact similitude is impossible in most relevant situations, so experience plays a significant role in determining what features can be relaxed without compromising the integrity of the model. Tetra Tech continues to build expertise in this area, with several PhD-trained experts in scale modeling. Our expertise in scale modeling is complemented by our abilities in computational fluid dynamics and other mathematics-based techniques, so we can provide a comprehensive turn-key solution to our clients.
Over the past several decades, we have continually incorporated process improvements into the many process technologies that we have been involved with. As a result, the gap between ideal and actual performance has closed dramatically. Optimization opportunities have become narrower and more challenging, and we have evolved our modeling approaches and measurement techniques accordingly. In addition to state-of-the-art instrumentation, such as high-speed videography or x-ray imaging, we now implement our own Tetra Tech Delta technologies including artificial intelligence and virtual sensors to bring real-time insight to our clients.
How do you validate that the model results are correct and meaningful?
Validation is a primary requirement of any modeling exercise. We validate modeling results against as many sources of data as possible—whether commercially available data from existing plants, results published in literature from past studies, our client’s own data from their installation, or empirical data from our own laboratory and simulation models. By building appropriately scaled physical models and using the right instruments, we can collect valuable data in-situ and use that data to cross-check against real-world performance of a process or its subsystems.
The data often are the most valuable aspects of any modeling project. To ensure the quality and integrity of the data we collect, we have a dedicated instrumentation team of adept PhD physicists and mathematicians who can identify the correct measurement techniques and sensors to gather the pertinent data from a system. In many instances, we have found that the right instruments—ones which offer the correct measurement technique, sensing range, accuracy, and repeatability—simply do not exist. In these cases, our team develops the necessary instruments to deliver the required measurements. This unique skillset offers our clients clear advantage in acquiring and gathering the data needed to resolve their challenges.
What advantages does modeling offer in analyzing processes?
Process modeling can add value at any point in the innovation chain—from proof-of-concept, gap closure, and scale-up phases, all the way to commissioning, commercialization, and even post-launch optimization and troubleshooting.
We always use our Leading with Science® approach, starting from the fundamental scientific principles. The customized modeling strategy that follows dictates how the model itself is employed, based on the specific goal of the project.
Tuned and validated process models—whether mathematical or physical—can offer numerous advantages over real-world tests. Systems such as those operating at elevated pressures or temperatures or with harsh substances or behind opaque walls are prime candidates for process modeling. Such systems can be analyzed in the laboratory with transparent and benign materials, or we can leverage Tetra Tech Delta technologies—including computational fluid dynamics simulations—within the computational space where safety regulations are of no concern. Modeling can quickly evaluate and optimize the performance of proposed geometries in a virtual environment where making changes has no repercussions on productivity or emissions.
What benefits of modeling have clients seen in their projects?
In one instance, a client wanted to develop a new flocculant additive for geotechnical stabilization and reclamation of a tailings pond. We used a model to test real chemical recipes and mixing equipment to evaluate flocculation quality. Modeling such processes allowed this client to test a multitude of recipes and physical configurations quickly, for significantly less cost than full-scale field tests, and with no risk to the surrounding ecosystem. The tests used a combination of physical and mathematical modeling that our team developed and constructed.
In another instance, we developed a first principles-based mathematical model to serve as a virtual sensor when the physical data of interest could not be measured and collected directly from the real process. The virtual sensor provides the process operators with valuable information that assists them in making decisions that keep the affected unit, in this case a chemical reactor, healthy.